Histoire de mon Extra indoor
J'ai toujours trouvé que les avions indoor d'acro n'étaient pas très beaux.
Ils sont souvent constitués de feuilles de depron découpée, aussi bien pour les ailes que pour le fuselage, le tout
rigidifié par des jonc en carbone.
Tout est en surfaces, il n'y a pas de volumes. Je me suis donc demandé s'il m'était possible de réaliser un avion
d'acro qui serait à la fois beau, rigide et léger.
Le nom du projet est "Extra indoor" car j'ai pris un Extra 300 comme source d'inspiration.
Début janvier 2020, je dessine une aile:
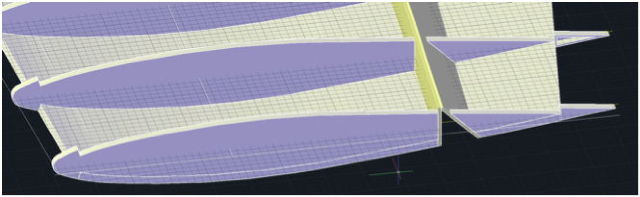
Les nervures et le recouvrement seraient
en polystyrène expansé de 2,5mm d'épaisseur à 0,95 grs/dm2 découpées à la CNC.
Les bords des parties avant et arrière
au niveau des charnières d'ailerons sont prévus en balsa 1mm d'épaisseur.
Les bords d'attaque et de fuite seraient
en impression 3D de PLA de 0,1mm d'épaisseur collés en partie sur le
recouvrement polystyrène et les nervures.
La terminaison de nervure au bord de
fuite serait un triangle en PLA de 2,5 mm (comme la nervure) avec la périphérie
en 0,6mm et le centre en 0,1mm.
Mi-janvier 2020, je décide de faire un essai:
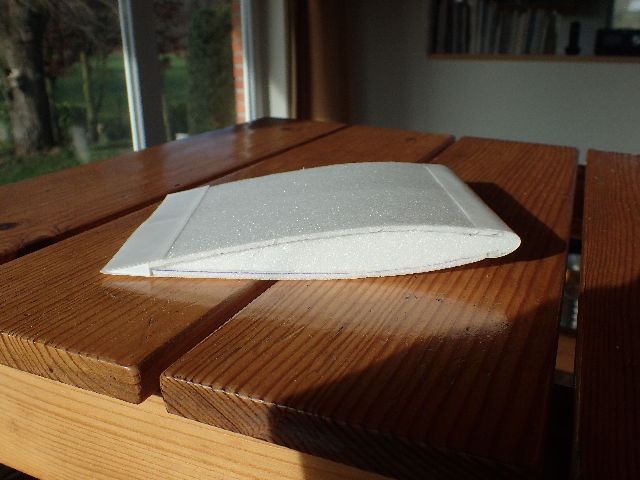
Je réalise un un bout d'aile de 10 cm
avec une corde de 15 cm, elle pèse 4 grammes.
Le bord d'attaque est imprimé en PLA de
0,1mm d'épaisseur.
Il est collé sur les nervures et sur le bord du recouvrement
en polystyrène.
Le bord d'attaque n'était pas facile à
coller car il faut le maintenir courbé.
Le bord de fuite est construit autour de
nervures en PLA collées sur les recouvrements (intrados et extrados) qui se
rejoignent (5 mm).
Deux feuilles en PLA de 0,1 mm sont
collées sur les nervures de fuite et les bords des recouvrements (intrados et
extrados).
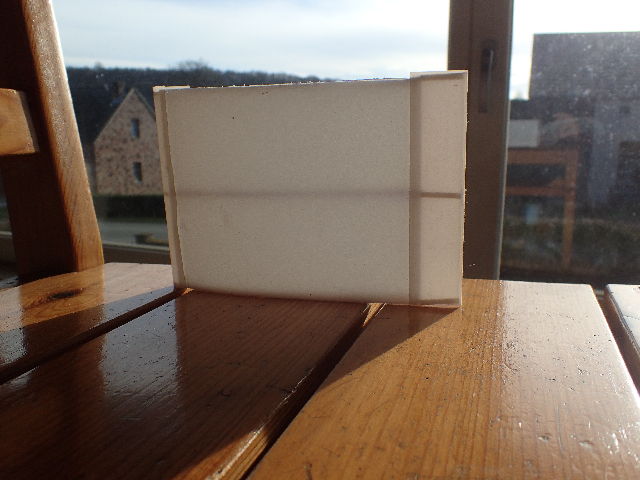
Voici un
bout de bord d'attaque de l'empennage horizontal (essai).
La partie plate fait
0,1 mm d'épaisseur et devrait être collée sur les nervures en polystyrène 2,5
mm.
Les autres parois font 0,6 mm d'épaisseur.
Il est difficile de peser la pièce mais
je l'estime à 0,1 gr/cm.
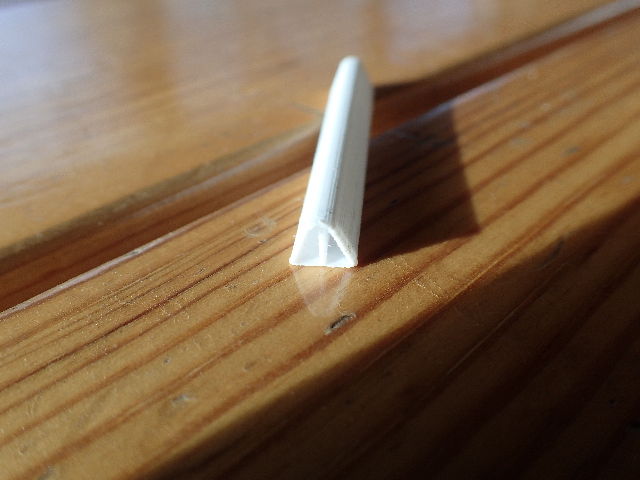
Le recouvrement de l'empennage horizontal ne peut pas être réalisé en polystyrène
2,5 mm car les nervures seraient alors extrêmement réduites, presque
inexistantes.
Le bord
d'attaque doit donc recevoir un recouvrement en PLA 0,1 mm mais il y a peu de
place pour venir le coller.
L'idéal
serait donc de pouvoir le courber sur le bord d'attaque.
J'ai donc fait un
essai avec un sèche-cheveux en plaçant la feuille de PLA sur un tube de carbone
de 4 mm.
Voilà le
résultat:
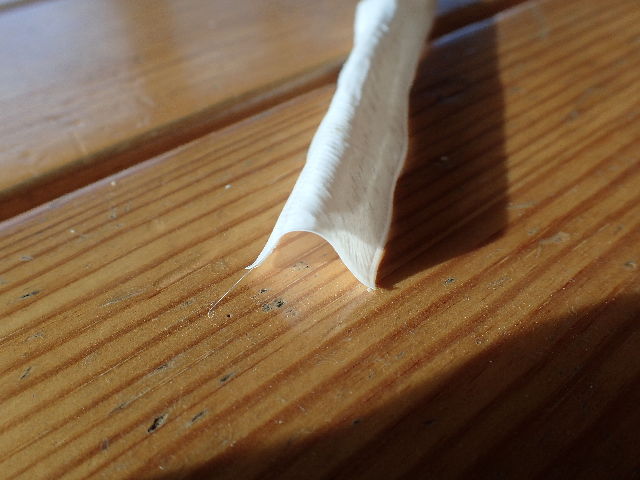
Cela fonctionne et il est aussi possible d'utiliser un fer à tendre les
recouvrements thermo-rétractables (thermostat 2).
Il est même possible de remettre à plat la feuille courbée, par contre il est
difficile de faire disparaître un pli formé par maladresse au sèche-cheveux.
Sachant que la température à atteindre pour courber la feuille n'est pas très élevée,
il doit être possible d'utiliser une forme de maintien de la feuille pour
éviter la formation de plis et de courber dans l'eau chaude.
Le bord de fuite ne pose pas de problème, les nervures en polystyrène finissent à une
hauteur de 5 mm et sont terminées avec une pièce imprimée en PLA.
Le recouvrement de 0,1 mm en PLA sont collés sur les terminaisons des nervures en
PLA. Les recouvrements d'intrados et d'extrados sont également collés l'un à
l'autre au bord de fuite.
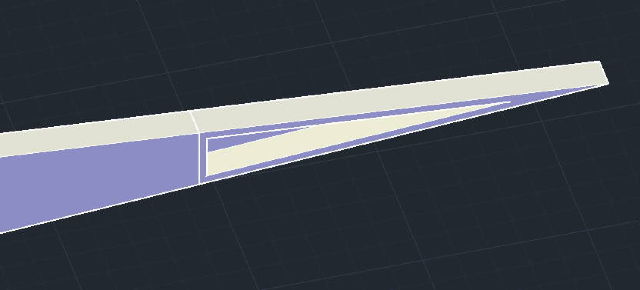
Je fixe mon projet à la réalisation d'un avion d'acro 3D de type Extra, de 90 cm
d'envergure et 22 dm2. L'aile ferait 30 cm à l'emplanture et 19 cm en bout
d'aile avec une épaisseur de profil de 12%.
Une telle aile sans ailerons devrait selon mes calculs peser 55 grammes et 63 grammes
avec ailerons.
L'aile de mon Discovery en EPP de 87,5 cm d'envergure et de 20 dm
2 comporte 51
grs d'EPP et 5,7 grs de carbone, elle pèse donc 56,7 grs.
La densité du polystyrène 2,5 mm de l'Intermarché a une densité de 38 grs/dm3
(pratiquement égale à celle de l'EPP).
La répartition du poids de mon Extra indoor serait donc:
recouvrement |
64% |
35 grs. |
nervures |
13% |
7 grs. |
bord d'attaque |
12% |
6,4 grs. |
bord de fuite |
11% |
6 grs. |
Total |
|
55 grs. |
Il est encore possible d'améliorer la rigidité ou d'alléger les éléments.
Les
feuilles de PLA imprimé de 0,1 mm des bords d'attaque et de fuite peuvent être
moins larges et collés à la cyano plutôt qu'à l'Uhu-por.
La rigidité peut être améliorée via des panneaux sur champ entre les nervures. On
peut aussi ajouter des des joncs de diamètre 0,3 mm comme longerons au-dessus
et en dessous des nervures.
Le 16 janvier, je n'aime pas trop le look du bord d'attaque mais pourquoi s'emmerder avec des feuilles
imprimées 3D de 0,1 mm en PLA puisqu'il suffit de chauffer le polystyrène 2,5 mm
de l'Intermarché (thermostat 3) pour le courber ?
En plus, je gagne 4 grammes sur l'aile de l'Extra. Reste à peaufiner
la technique de recouvrement sur plusieurs nervures.
Le 24 janvier
Le 15 février, il reste à :
- dessiner le dessous du fuselage à l'avant et derrière l'aile,
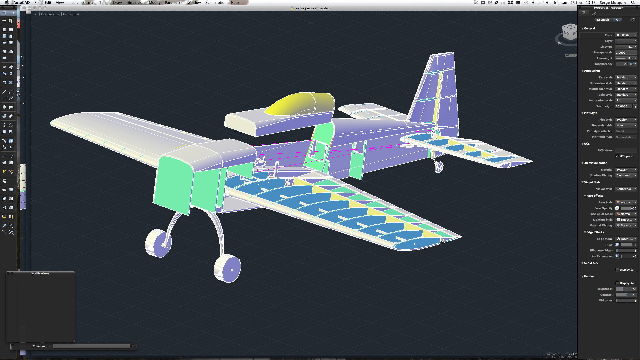
- découper le polystiène,
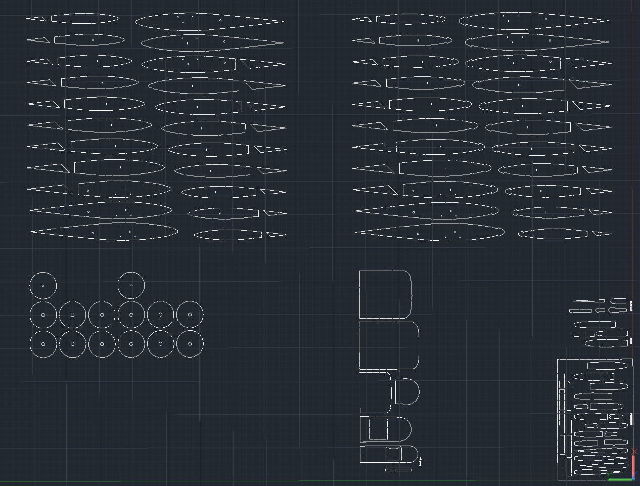
- imprimer les pièces en PLA,
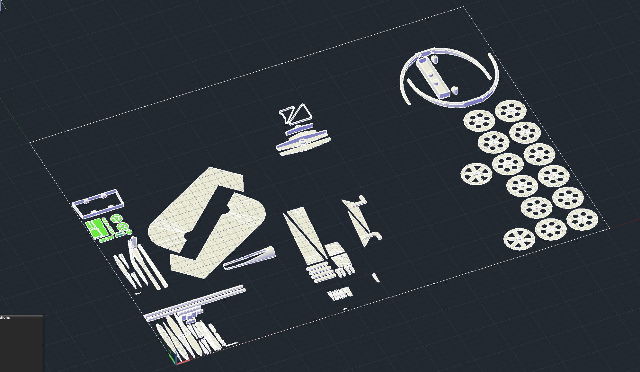
- commencer la construction pour affiner la position à donner à la motorisation, au pack
LiPo et à la radio,
- dessiner la mise à jour et le capot moteur,
- finir la construction.
Le 23 février
- de nombreuses pièces en PLA sont imprimées
- le polystirène est découpé:
roues train principal diamètre 50 mm / largeur +/- 19 mm
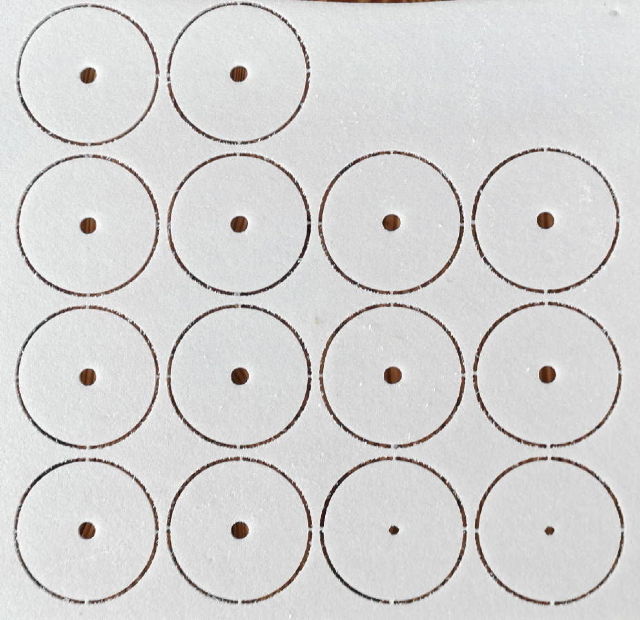
nervures aile / envergure 900 mm / corde emplanture 300 mm /corde saumon 190 mm
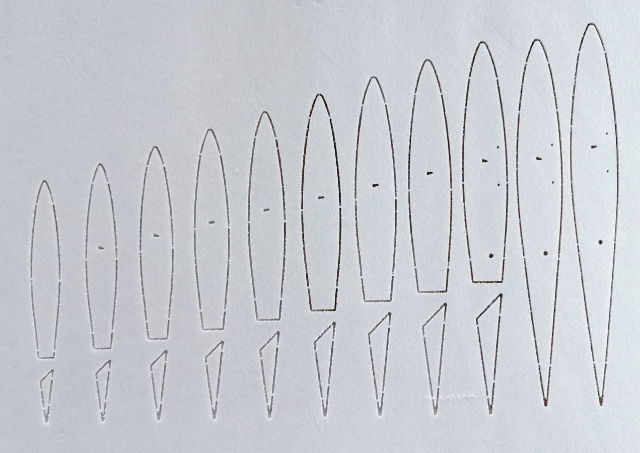
fuselage longueur sans moteur ni capot 775 mm
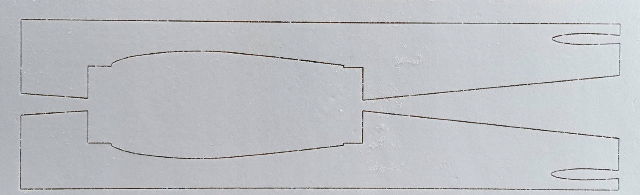
couples fuselage largeur max 94 mm et pièces diverses
Le 27 février
support des servos de direction et de profondeur
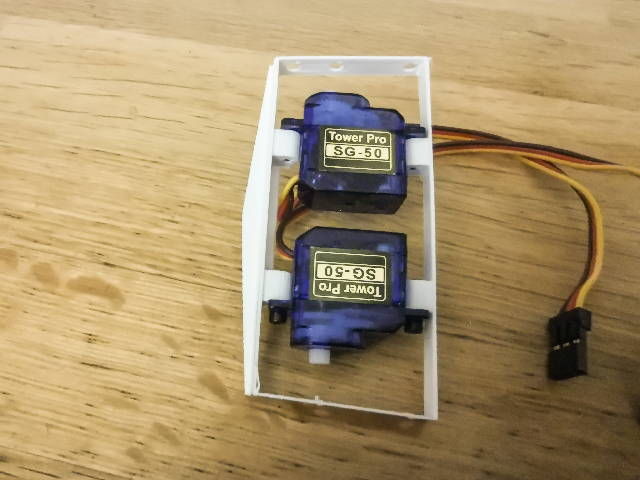
train
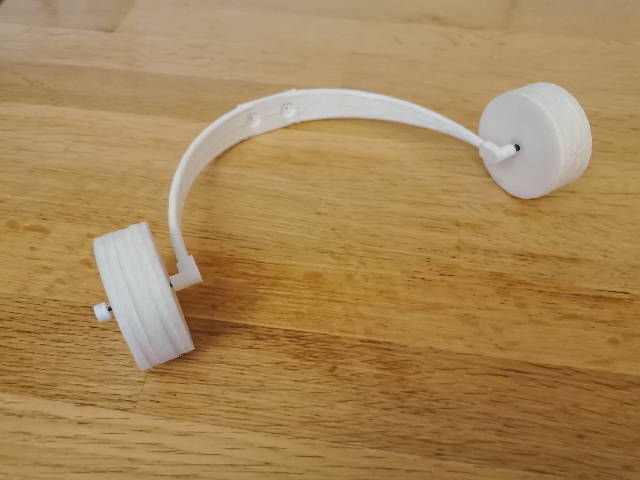
gouvernail de direction
Le 14 mars, je constate que tout cela est fragile et pas facile à monter.
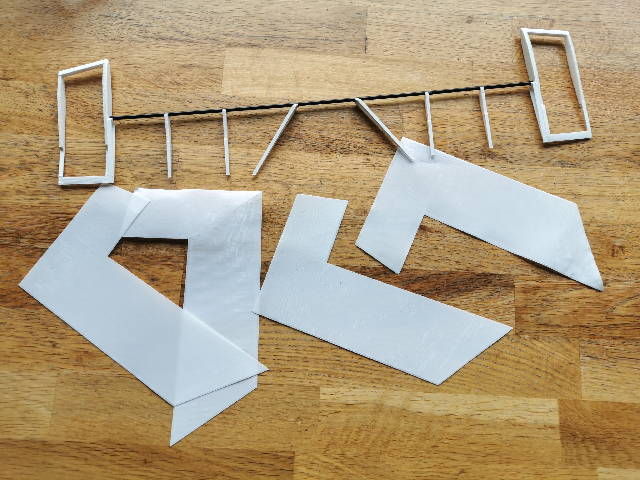
le début de la construction se fait sur un bâtis de montage (4 pièces en raison de la
taille)
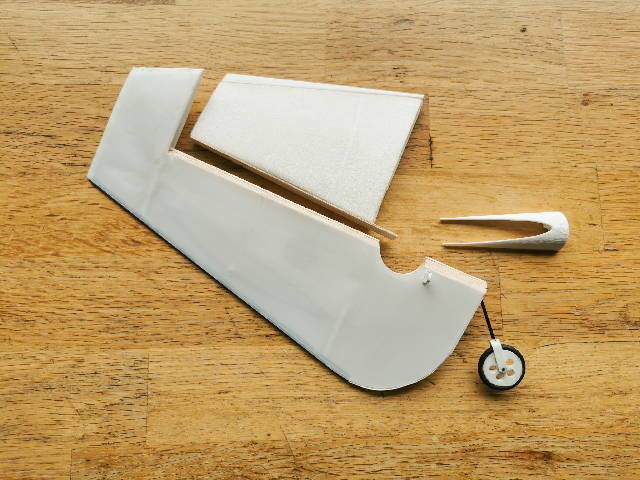
J'ai été amené à changer les plans du gouvernail de direction et d'adjoindre une CAP de
0,8 mm et une latte en carbone pour maintenir l'alignement des nervures et du
bord de fuite.
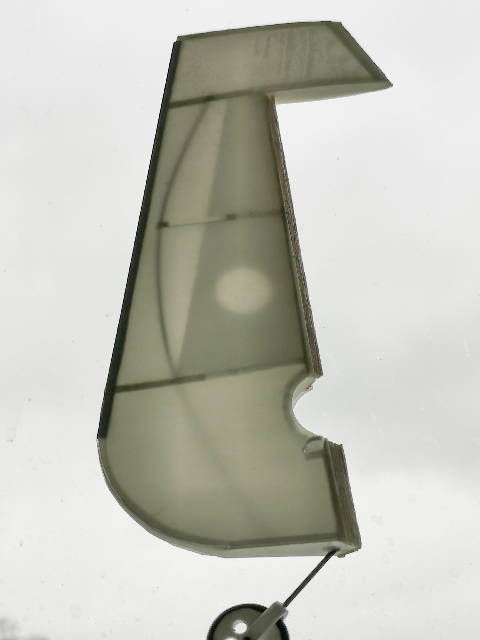
Il est difficile de conserver l'alignement des nervures lors du recouvrement du gouvernail
de profondeur.
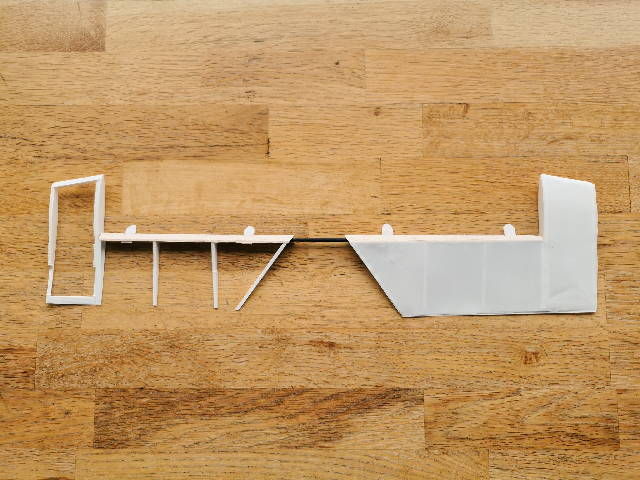
J'avais choisi du cordonnet en coton, c'est très solide mais fragile quand la cyano
fige le cordonet. Il ne peut y avoir de colle là où le cordonnet serait amené à
fléchir.
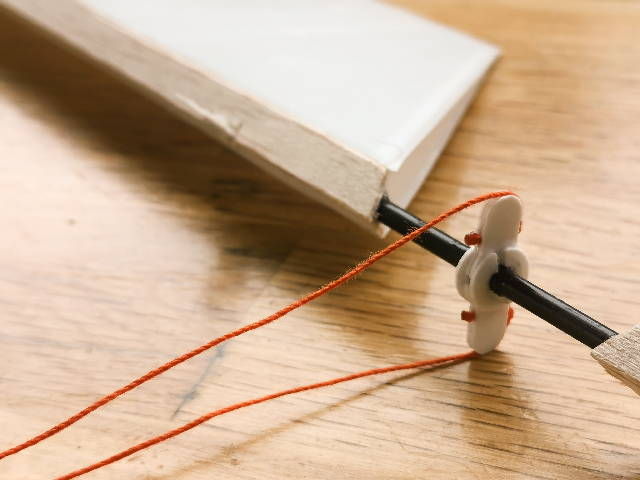
Pour ne pas tout recommencer lorsque le cordonnet a cassé, j'ai imprimé de petits pontets.
Le fil est guidé vers les rainures du guignol dans le bon axe et libre de colle
où il fléchit.
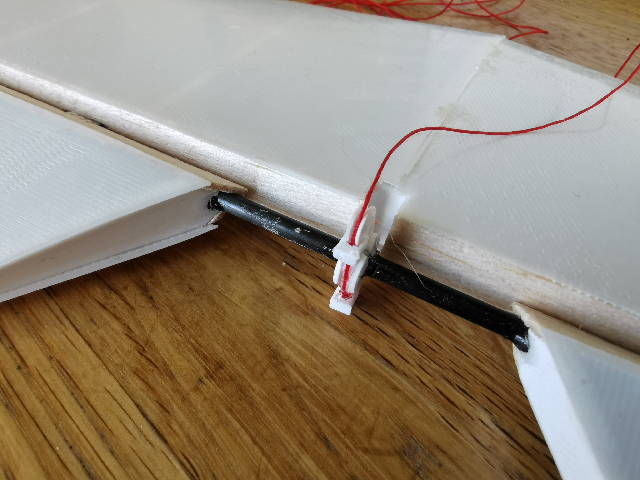
Comme pour le gouvernail de profondeur, difficile de conserver l'alignement des
nervures lors du recouvrement du stabilisateur
Le 17 mars
Le 19 mars, le bord d'attaque des ailes est courbé au fil chaud.
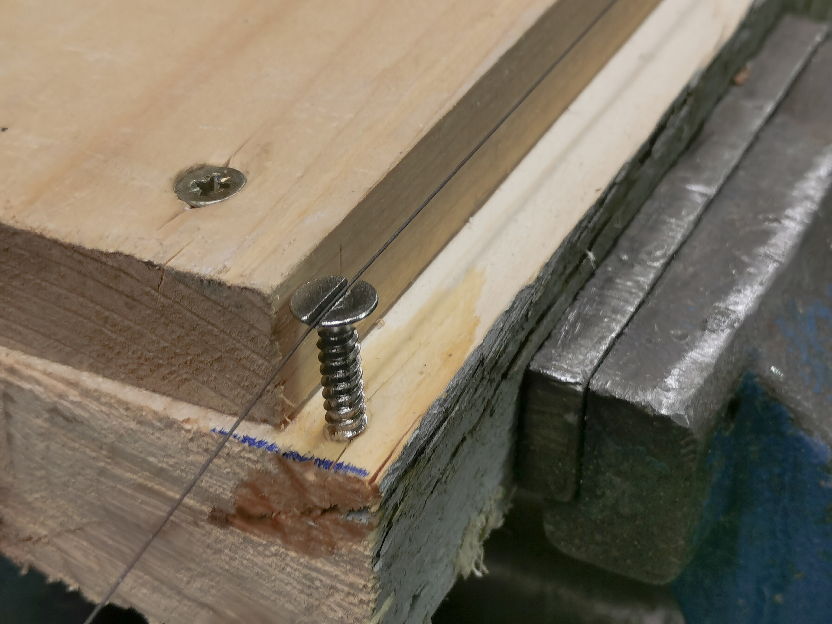
L'épaisseur évolutive de l'aile et donc du bord d'attaque engendre une courbure lorsqu'on
opère la mise en forme. Il faut maintenir le bord d'attaque aligné pour le
recouper à largeur constante.
Le 22 mars, un banc de montage permet de coller les nervures de l'aile sur le bord, puis de coller
le bord d'attaque.
Le 23 mars, un second banc de montage permet de coller le recouvrement en polystyrène.
Le 24 mars, les nervures centrales sont ajoutées.
Le 26 mars, jonction des ailes gauche et droite.
Le 27 mars., les ailerons sont installés.
Le 13 avril., j'effectue des essais de réalisation de la partie supérieure courbée à l'arrière du
fuselage. Je fini par utiliser une latte en aluminium et des couples découpés à
la CNC comme gabarit.
Je devrai trouver le moyen d'améliorer la finition et trouver le moyen de
maintenir le tout en place pendant le travail.
Le 15 avril, début de la réalisation du fuselage.
Le 16 avril, installation de l'empenage.
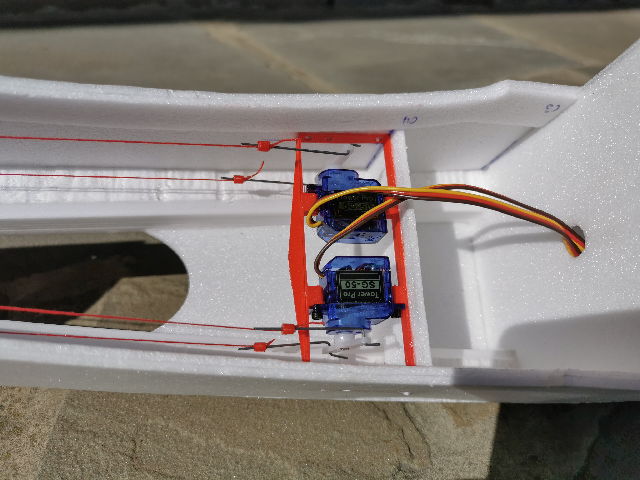
Le bras de servo d'ailerons doit être rallongé pour obtenir un débattement suffisant.
Le 17 avril, l'extra est presque terminé.
Le 25 avril, je réalise le capot par thermoformage.
Le 26 avril, je réalise les moules pour le thermoformage du cockpit.
Le 27 avril, je réalise les moules pour le thermoformage du cockpit.
Je démoule et constate que le mortier réfractaire que j'ai utilisé perd des grains
au frottement.
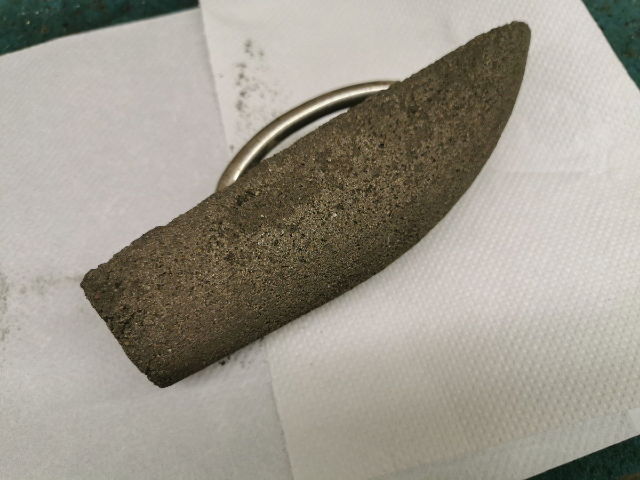
J'applique une couche d'enduit de réparation pour plâtre, le problème est résolu.
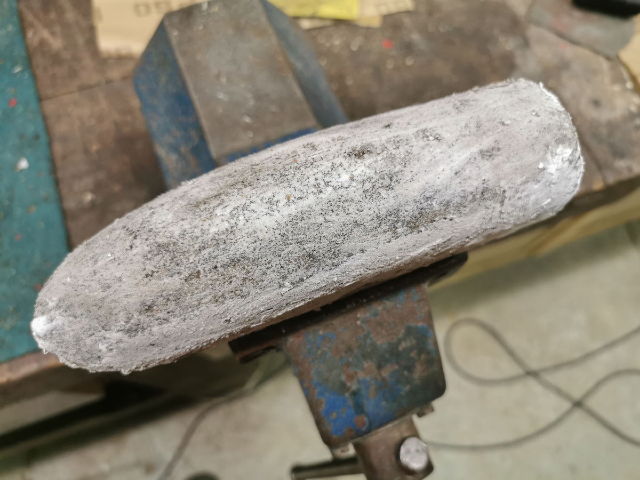
Je découpe la planche d'après le gabarit et je fais quelques essais infructueux
avec des bouteilles d'eau récupérées. Je n'ai rien d'autre sous la main d'assez
fin, ce sera pour plus tard.
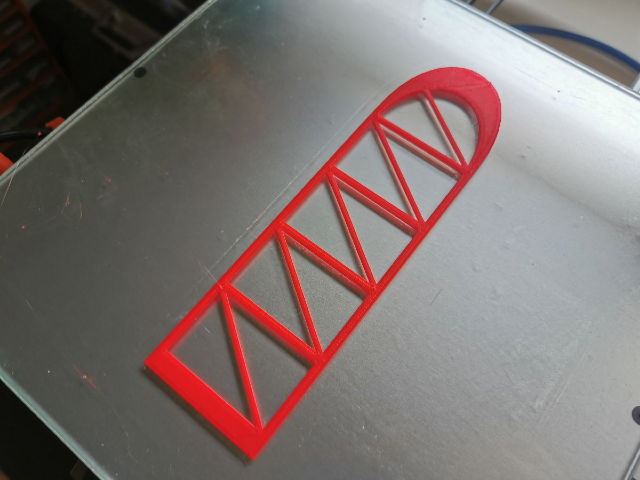
Comme j'ai reçu le moteur, je l'installe ainsi que les fixation avec de petites
équerres en PLA et du velcro.
Le 1 mai.
Je trouve que le thermoformage à la vapeur a fonctionné pour le capot moteur mais
de manière imparfaite. Pour le cockpit, ça ne fonctionne pas du tout, j'obtiens
des plis.
J'effectue des essais au décapeur thermique et j'ai toujours des plis
et, en plus, le plastic blanchit à certains endroits.
Je décide alors d'employer
les grands moyens et je me lance dans la fabrication d'une boîte pour
thermoformer par aspiration.
J'ai à nouveau fait des essais en chauffant au décapeur thermique mais cette technique
ne semble pas fonctionner correctement. Je ne dispose plus de matière et les
magasins sont fermés.
Le 2 mai.
Je réalise que je dispose de feuilles en plastique transparent que l'on trouve en
papeterie et dont on se sert pour réaliser des couvertures de documents
brochés.
Je trouve sur internet l'information que ces feuilles rodoïd sont
thermoformables. Je réalise donc un cadre pour maintenir la feuille durant
l'opération.
Je devrai réaliser 8 essais avant de pervenir à un résultat
convenable.
L'utilisation du décapeur thermique conduit souvent à des températures différentes en divers
endroits, ce qui engendre des tensions trop fortes qui conduisent à la
formation de trous et donc à l'arrêt de l'aspiration.
J'ai fini par trouver sur internet le conseil de chauffer la feuille au four pendant 1 minute à 200° et,
moyennant le respect de quelques règles supplémentaire, cela fonctionne.
Il
faut passer très vite du four à l'aspiration pour que la feuille garde sa
température et l'enfoncer directement jusqu'à ce que le cadre soit en contact
avec le socle d'aspiration.
De plus, il faut que la feuille descende plus bas
que le bas de la pièce à thermoformer, faute de quoi le bas de la pièce est
remplacé par un karman.
Le 3 mai, mise enplace du cockpit.
Le 28 mai.
J'ai enfin reçu le variateur de vitesse 15 Amp et l'hélice et je découvre que le
variateur ne fonctionne pas correctement avec l'hélice 11x3,8.
J'ai essayé tous les réglages possibles en vain, parfois il démarre et parfois
il hésite à l'infini.
J'installe donc un variateur 25 Amp dont je disposais et
je cherche la position de l'accu qui mettra le centre de gravité au bon endroit.
Malheur! J'ai certainement fait une erreur de calcul car l'accu doit aller dans
la partie avant de l'aile alors que j'avais allongé l'avant du fuselage et prévu
2 trappes.
J'avais d'abord voulu obtenir un poids de +/-250 grs mais petit à petit j'ai été amené
à reconsidérer mon espoir et depuis le 20 avril je savais qu'il atteindrait au
moins 360 grs.
Il en fait 425 ! C'est ce que j'appelles se planter en beauté.
Le 30 mai.
Malgré le vent fort et en rafales, je décide de faire un vol d'essai en décollant au
beau milieu d'un champ de froment (au cas où).
Le 13 juin.
Je décolle enfin du terrain et fais un bon vol malgré le vent mais le train s'avère fragile à l'atterrissage.
Le 17 juin.
La possibilité de démonter l'aile présente un intérêt pour le rangement de
l'avion. Toutefois, devoir l'effectuer pour changer d'accus est assez pénible.
Aussi, je décide de modifier la partie inférieure de l'aile pour pouvoir y
insérer l'accu sans démontage.