Histoire d'un crash
Depuis que j'ai ce Ka 8b, je trouve qu'il vole mal, qu'il a une fâcheuse tendance à décrocher en virage et
qu'il est alors difficile à récupérer.
A l'occasion de ce crash, un peu par hasard, je me rends compte que les ailerons ont plus de débattement vers le bas que vers le haut.
Cela me paraît bizarre et je vérifie qu'en effet c'est le contraire de ce qui est prévu mais avec les bonnes valeurs de débattement.
Je comprends alors que j'avais sans doute réglé les débattements et que, constatant ensuite que ceux-ci étaient inversés, je m'étais contenté d'inverser le sens des servos.
Evidemment, cela explique pourquoi mon planeur avait tendance à décrocher en virage et était alors capricieux.
Je n'aurais pas dû passer devant le soleil alors que je volais lentement, cet excès de confiance s'est transformé en vrille dont je n'ai pas compris le sens de rotation et dont je n'ai pas réussi à sortir à temps.
Je ne pensais pas reconstruire ce planeur car le recouvrement des ailes présentait des fentes. Un aileron ne fonctionnait que dans un seul sens sans que j'en comprenne la raison.
J'ai donc commencé par examiner le servo de cet aileron pour découvrir que c'était simplement le contreplaqué-support de servo qui était décollé.
J'ai ensuite enlevé les parties fendues de l'entoilage pour examiner la structure des ailes. Elles ne présentaient aucun dommage et je me suis contenté de recoller le support de servo en contreplaqué.
Les dégâts au fuselage étaient évidents et importants et je n'avais pas le courage de démonter tout l'avant pour en faire les plans et refaire les pièces pour la reconstruction.
Cependant, il me paraissait possible de simplement recoller ensemble les morceaux de fuselage pour ensuite consolider les parties de contreplaqué explosées.
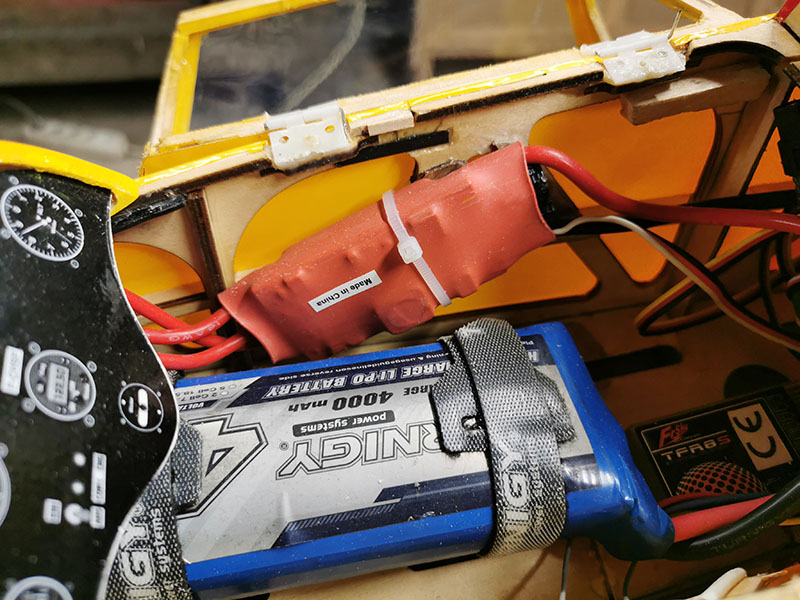
J'ai utilisé des bouts de plaque de carbone de 1 mm d'épaisseur et de la colle époxy 4 minutes car je suis un homme pressé.
La partie capot moteur en fibre de verre avait souffert aussi: le gelcoat explosé par endroits laissant voir le tissus de verre mou.
J'ai rigidifié la fibre à la colle cyano, poncé et, sur les conseils de Sylvain, remis du gelcoat.
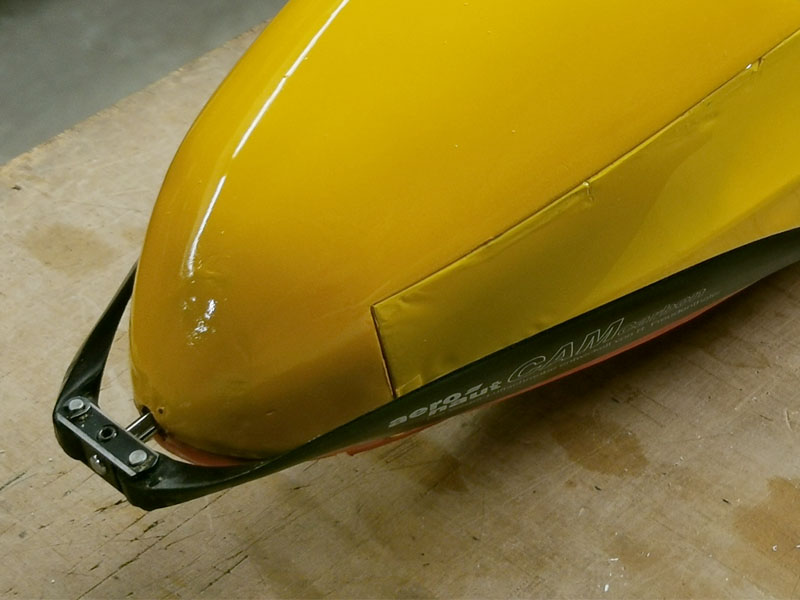
Comme pour le reste, le résultat n'est pas parfait mais un planeur imparfait vaut mieux que pas de planeur du tout.
D'autant plus qu'à chaque nouvelle avancée du travail, j'avais plus de mal à accepter l'idée de ne pas pouvoir terminer.
Je ne savais pas que je n'avais alors fait que la partie la plus facile.
Il ne restait plus qu'à refaire la bulle dont la partie avant gauche était en morceaux et présentait un trou.
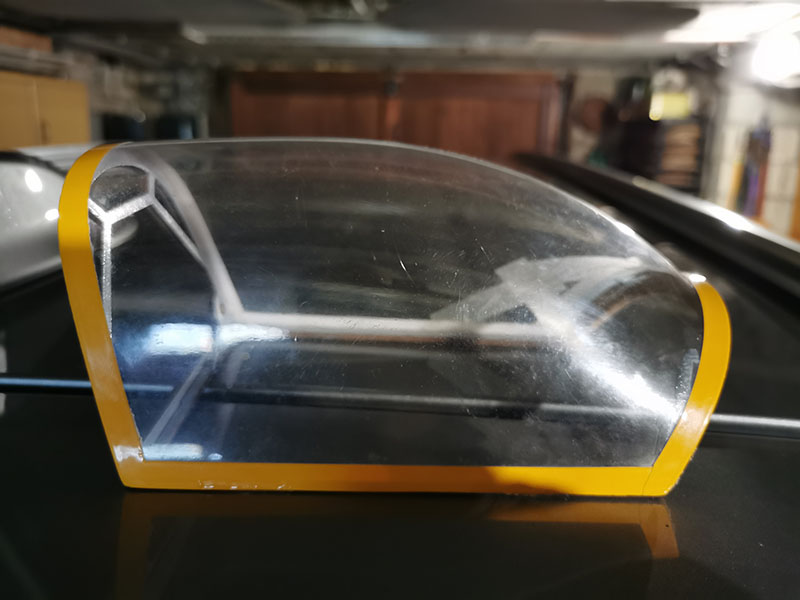
Dès lors, il était évident qu'il me faudrait faire un moule et thermoformer une nouvelle bulle. J'ai mis beaucoup de temps avant de décider de la méthode.
J'ai commencé par scanner les parties en contreplaqué pour en faire les plans et les découper à la machine CNC.
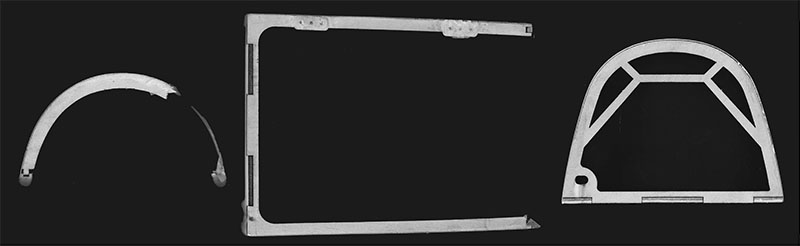
J'ai assemblé les pièces en utilisant le fuselage reconstruit comme support-guide. Il restait à trouver la matière pour faire le moule et le plastique thermoformable pour la bulle.
Mes recherches m'ont amené à acheter le plâtre dur Gédéo pour coulage et le plastic thermoformable pour création artistique chez Schleiper, je ne ferais plus le même choix aujourd'hui.
Couler le plâtre dans la bulle impose que celle-ci soit étanche mais il faut aussi trouver le moyen de diminuer la quantité de plâtre par l'insertion d'un support étanche, lui aussi.
En effet, la bulle est assez grande et l'ajout d'un support permet d'économiser le plâtre et présente aussi l'avantage de diminuer le temps de séchage.
J'ai alors dessiné un support et des plaques-bouchons en prévision d'une impression 3D. J'ai aussi réalisé un support en contreplaqué afin de maintenir la bulle d'origine lors du coulage.
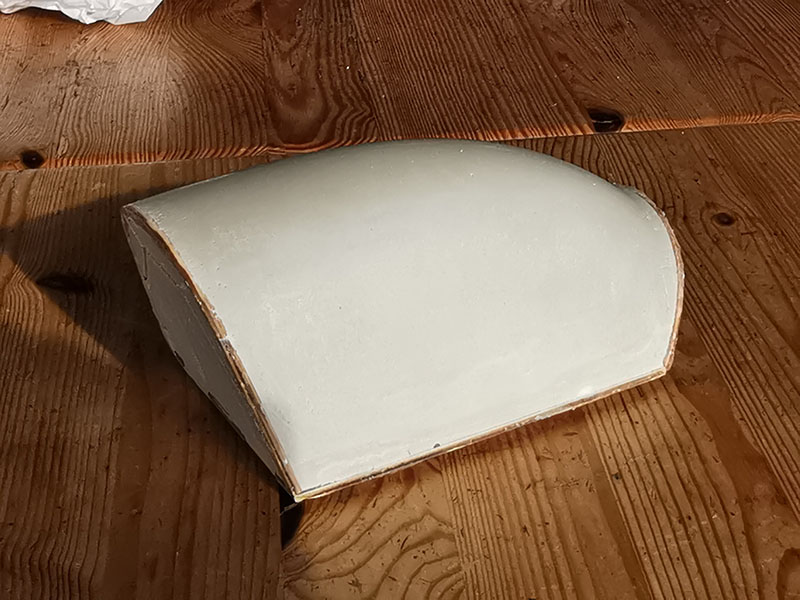
Le plâtre est ajouté à l'eau à raison de 2 volumes pour 1 volume d'eau, le tout laissé au repos durant une minute avant d'être mélangé puis coulé.
Le volume d'eau peut être évalué facilement en remplissant le moule et en y enfonçant le support. Le volume d'eau restant dans le moule est le volume d'eau à utiliser.
On peut y ajouter une quantité en réserve en cas de fuite lors du coulage. En effet, l'ajout du plâtre dans l'eau ne modifie presque pas le volume total.
J'ai commis l'erreur de mettre un peu moins que 2 volumes de plâtre dans l'eau, c'est une faute à éviter car le séchage qui devait durer quelques heures a pris une semaine.
Je pensais que le plâtre était simplement froid au touché mais, en réalité, il n'était pas sec.
Cela a certainement une incidence sur le thermoformage car la feuille plastique se refroidit plus vite et refuse alors de s'allonger suffisamment.
Voici comment j'ai procédé:
Cliquez dans l'image
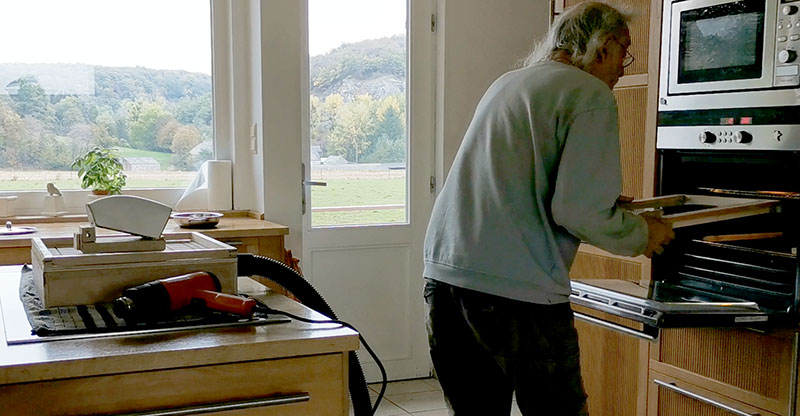
La table d'aspiration est celle que j'ai réalisée pour le
thermoformage de la bulle de mon extra
"indoor"
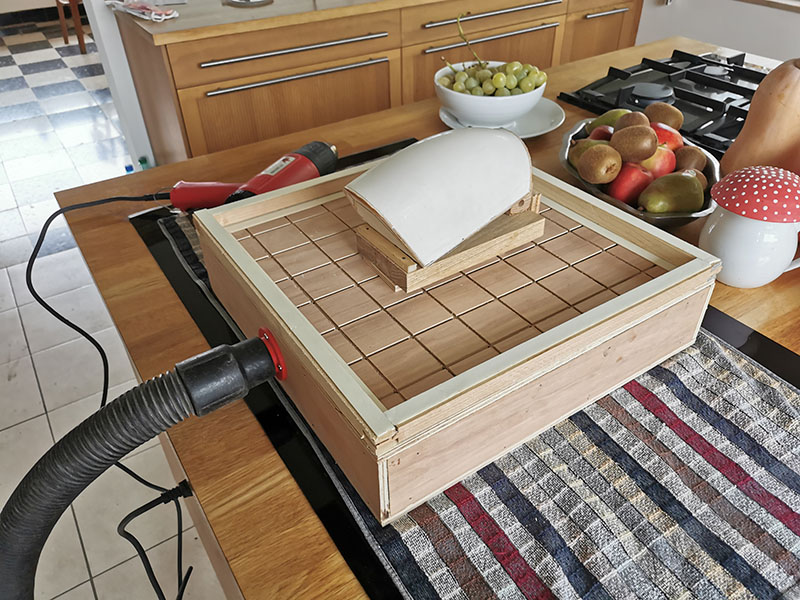
Pour mes premiers essais, je portais la feuille plastique à 170°.
Je ne parvenais pas à amener la feuille sur la partie basse du moule et j'utilisais alors un décapeur thermique pour tenter de réchauffer et former le bas de la bulle.
A chaque fois, soit j'obtenais un trou réduisant à néant l'aspiration, soit le plastique blanchissait.
A ce stade, je ne savais pas si le moule était en cause ou si c'était le plastic et j'ai consulté pas mal de site sur internet.
J'ai fini par trouver que le nom utilisé pour le plastic destiné à faire des verrières était "rhodoïd", j'en ai trouvé chez Weymuller et j'ai fait une comparaison.
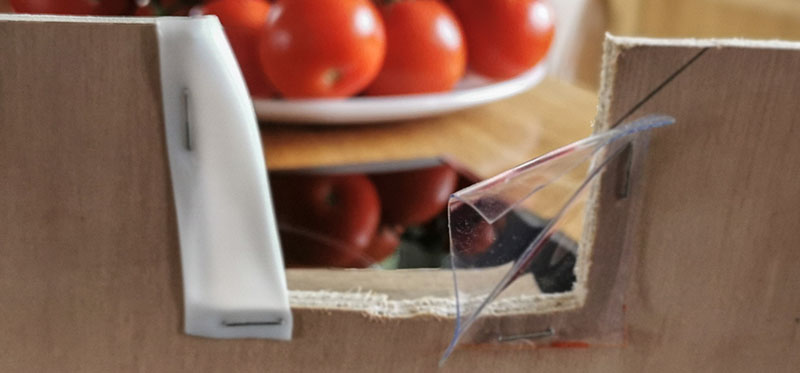
A gauche, le plastic de chez Schleiper. A droite, le rhodoïd de chez Weymuller. Le rhodoïd tient au delà de 210°.
Après un nouvel essai raté parce que je ne parvenais pas à former le bas de la bulle, j'ai réalisé un cadre de maintien de la feuille plastique plus grand.
Il fallait que je réussisse car je n'avais plus assez de matière pour deux tentatives. Malgré tout, en ayant laissé le rhodoïd à 210° durant une minute, l'aspiration ne parvenait pas à former le bas de la bulle.
J'ai alors compris que la dépression se répartissait sur la partie de la feuille non encore formée dont les bords étaient assez loin du moule.
Tentant alors le tout pour le tout, j'ai remis la feuille au four qui a fini par se retendre dans le cadre pour un dernier essai.
Dès l'arrêt du mouvement marquant la formation de la bulle sur le moule, j'ai utilisé mes deux
avant-bras pour enfoncer la feuille vers le bas, réussissant finalement ainsi une bulle satisfaisante.
Tant que j'y étais, autant réparer aussi le pilote en mille morceaux avec un grand trou dans la tête. Il a maintenant un look de lépreux qui va bien avec le reste.
Cette réparation à l'arrache a tout de même pris un mois.